I came across an interesting problem while doing some preliminary models. I was modeling a cantilever member (10" x 10" x 60"). I had fixed the nodes at one end for all DOFs and applied a temperature change of 50 F. One would expect the stress in the member to be uniform and approximately zero. However, the plot of the stresses in the long dimension of the member showed there to be some variation in the stresses given by the model.
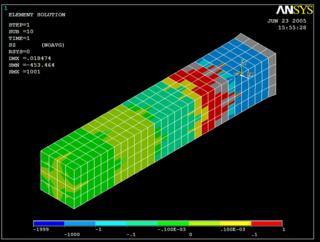
Note that the red contour indicates stresses between 0.1 and 1 psi. The gray contours are stresses greater than 1 psi. While high stresses should be expected near the support, such areas of higher stress at a distance of 16 in. away from the support was unexpected.
Since Poisson's effects were suspected as the cause for the variation in stresses, the boundary conditions were changed to the arrangement shown below. Only the center four nodes at the end were restraned in all DOFs. The rest were only restrained in the Z-direction (long dimension of the model).
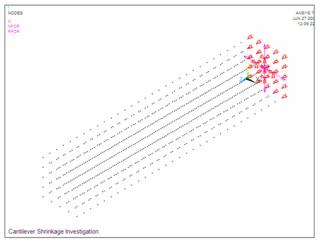
The analysis was run again with the new BCs and the same temperature load applied. The stresses in the model were found to be more consistent as well as clloser to the correct value of zero.
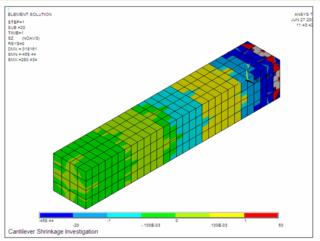
Note that with the improved BCs, the model only gives stresses above 1 psi within 12 in. of the end support. This is consistent with St. Venant's principle which states that at a distance b away from the load stress are uniform, where b is the width of the section being loaded. Points within a distance b exhibit higher stresses and the stresses are not uniformly distributed (Beer & Johnston 1992).
We can see then that poisson's ratio is significantly effecting the results derived from the model. Thus, I set Poisson's ratio equal to zero and repeated the analysis. The stresses at a section through the middle of my model specimen are shown below. The stresses observed are now significantly more uniform and are generally closer to zero.
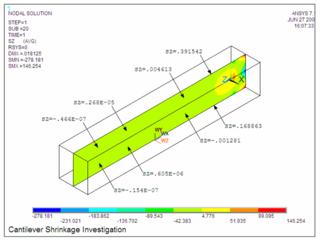